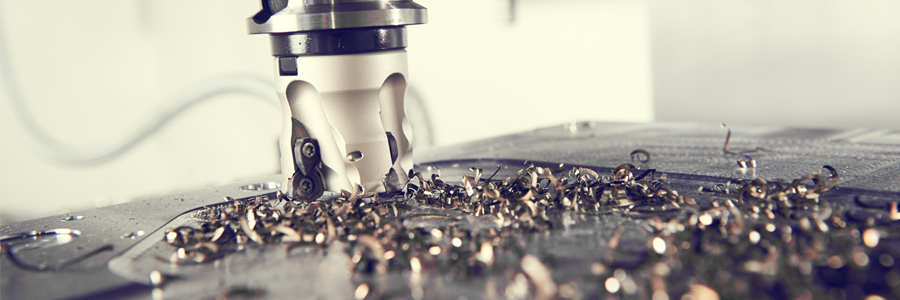
自動工具交換装置の付いたマシニングセンタは、金属加工の現場に多く普及しています。その種類は「横型」「立型」「門型」「5軸」など様々あり、それぞれに特徴があります。種類別にメリット・デメリットなどを簡単にわかりやすく解説しています。
マシニング加工とは
マシニング加工とは、「マシニングセンタ(Machining Center)」と呼ばれる機械を使用して、複数の切削加工に使用する工具を自動的に切り替えながら行うことです。
工作機械を使用して金属の不要な部分を除去し、目的の形に成形することを切削加工といいます。切削加工は、加工する工作物を固定して工具を回転させる「転削」と、工作物を回転させて工具にあてる「旋削」に分かれます。切削にはフライス加工・中ぐり加工・穴あけ加工・ねじ加工などの作業があり、例えばフライス加工ならフライス盤、穴あけ加工にはドリル、ねじ加工ならバイトなどそれぞれの工具を使用します。これらの複数の工具が付いており、工具を切り替えながら加工できる機械がマシニングセンタです。
図面(CAD)をもとに削る方向や刃物を動かす速度、回転数などをプログラムして人が行う作業を最小限にすることができるため、作業効率が上がり大量生産にも向いています。また人が刃物に触れる回数が少なく、安全性も上がります。
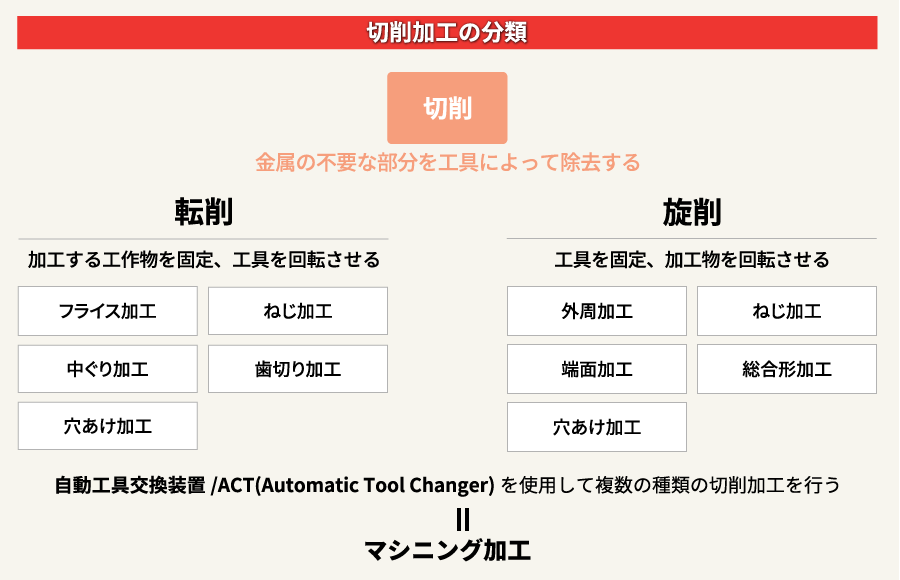
同様に3DCAD/CAMソフトウェアを使用し、プログラムで制御している「NCフライス盤」という機械もあります。フライス加工だけではなく、中ぐり、穴あけなどの加工も可能でマシニングセンタと似ていますが、マシニングセンタには「自動工具交換装置/ATC(Automatic Tool Changer)」が付いており、工具の切り替えが自動で行えるという点が最大の特徴です。1つの素材を一度固定(チャッキング)すると、いろいろな方向から工具を当てることができ、材料の位置を調整する手間を省けますので、多工程のある加工に向いています。
マシニングセンタの種類
マシニングセンタの共通の特徴は、複数の工具を自動的に切り替えてプログラミングによる数値制御が可能、繰り返し精度が高く量産加工に最適であることです。工具の付いている方向や動きによって種類が分かれていますので、代表的な4種類についてご紹介します。
横型マシニングセンタ
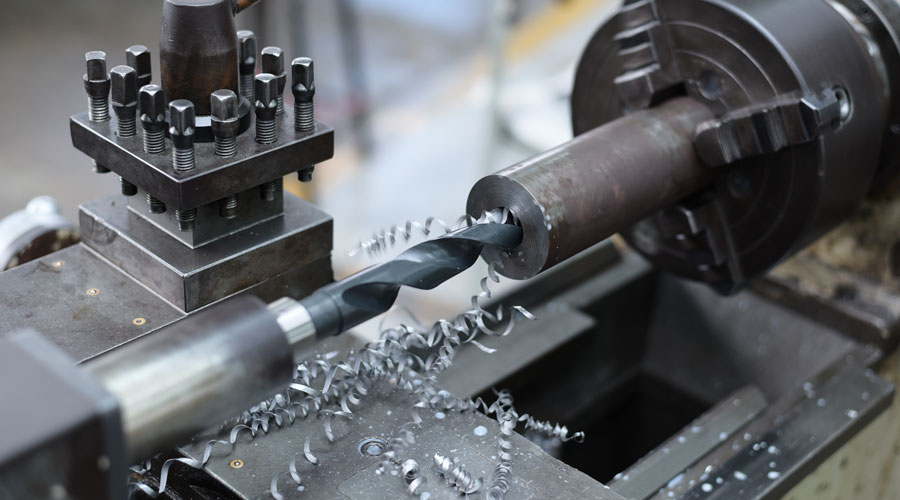
最初に開発されたマシニングセンタが横型です。刃物を取り付ける回転軸(スピンドル)が横向き(地上に対して水平方向)に取り付けられています。刃物をX軸・Y軸・Z軸方向に、テーブルを回転B軸に沿って動かすことが可能で、加工物の4面を同時に、複数個加工することができます。段取り(ワークの付け替え)が少ないため、位置ずれによる加工精度の低下を防ぐことができます。加工物を横から削ることで削り屑が下に落ちて溜まりにくく、刃物が食い込んでしまうといった不具合を避けることができるため、長時間の無人稼働にも向いています。
横型マシニングセンタのデメリットとしては、加工物(ワーク)を支える力が必要なため、重い材料の加工には適さないことや、切削油(クーラント)も下に落ちてしまうため加工面に届きにくいといった点が挙げられます。また機械自体が大きく、プログラムを組むのが難しいといったことから導入の際のハードルがやや高くなります。
立型マシニングセンタ
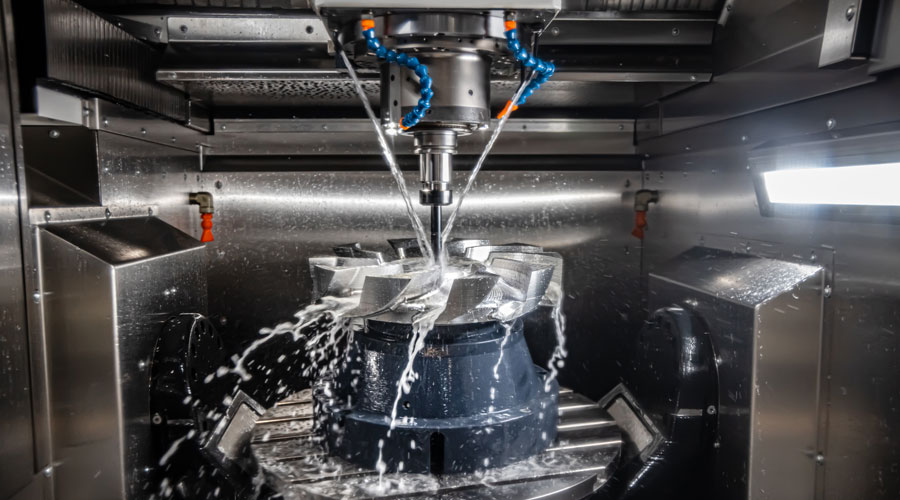
刃物のスピンドルが横向きに付いている横型に対して、縦向きに付いているのものを立型と呼びます。一般的には、テーブルがX軸、Y軸の水平方向に移動し、回転軸が垂直方向に移動することで、3軸での加工が行える「テーブル駆動式」になっています。主軸がX軸、Z軸に動き、テーブルがY軸に動く「主軸駆動式」もあります。加工物(ワーク)を上方向から切削するため、設計図と見比べながら作業がしやすい点が長所です。横型と比べて機械のサイズが小さく、設置スペースを節約できます。導入コストも比較的低いため幅広く普及しています。
デメリットは、機械が小さいため大型部品の加工には適していないということです。また工作物の上部から加工を行うことによって切り屑が加工物の上に溜まってしまうので、圧縮空気の吹きつけや潤滑油剤を用いて切りくずをはけさせる必要があります。
門型マシニングセンタ
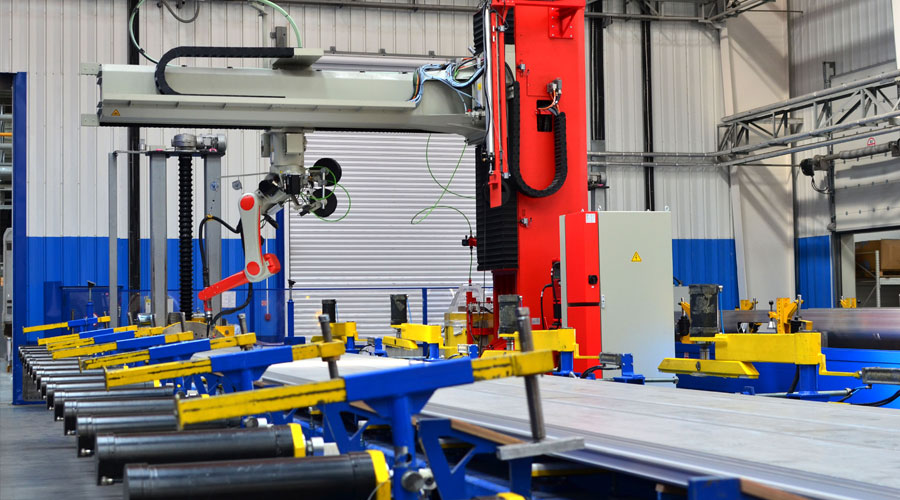
主軸を支える構造が「門」の形をしていて、回転軸が門の天井部に下向きについているマシニングセンタです。通常のテーブルに乗らない数メートル級の大物ワークを加工することができ、段取り(ワークの付け替え)が不要で作業効率が上がります。上下左右、そしてねじれなどの荷重に対して剛性を持ち、重切削に耐えることができるのが特徴です。高精度の位置決めができるので、航空機用構造部品、半導体製造装置の部品、自動車の部品など精度が求められるものに幅広く使用されています。設備が大がかりなため設置スペースが必要になり、導入コストも高くなります。
工具の動き方には3種類あり、最も一般的なのは、「クロスレール固定式」とよばれる、主軸が上下左右(Y軸・Z軸)に動き、テーブルが前後(X軸)に移動する方法です。その動きに加え、主軸を支えるレールが上下(X軸)に移動する「クロスレール移動式」や、主軸を支える「門」自体が前後(X軸)に移動する「ガントリー式」もあります。
5軸マシニングセンタ
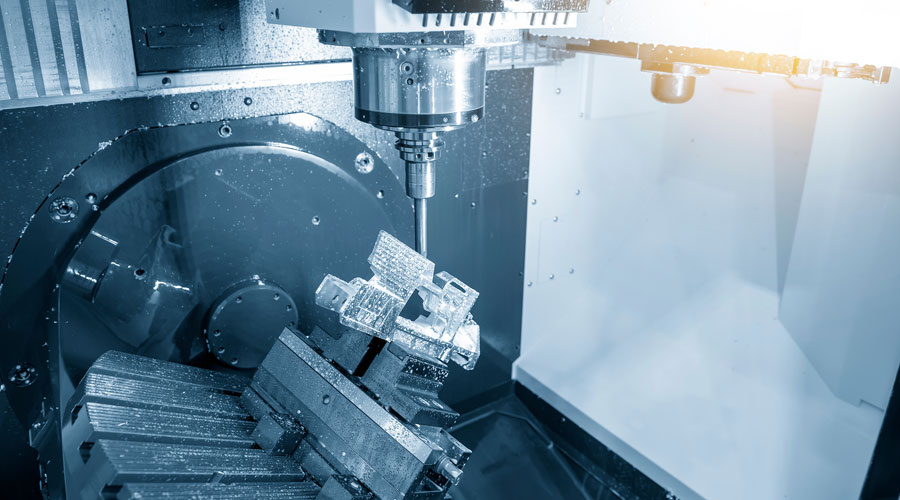
刃物を動かす3軸(X軸・Y軸・Z軸)に、回転傾斜軸が2軸追加され、合計5軸で切削加工を行うマシニングセンタです。回転軸があることによってより複雑な加工が可能になり、通常は複数回段取りをしなければならないような加工も、一回の段取りでスムーズに行えます。このことにより、段取り替えによる誤差なども防ぐことができます。刃物を加工面に対して傾けてあてることもできるため、刃物のついたツールと加工物の干渉を避けることが可能で、刃物の剛性を上げる効果もあります。
加工方法は2種類に大別でき、2つの回転軸を任意の角度に位置決めし、直線軸3軸で加工する「割り出し5軸加工」と、3つの直線軸と2つの回転軸とを同期させて、同時に3次元曲面を加工する「同時5軸加工」があります。
同時5軸加工ではワークの角度調整回数が最小限になる一方、それぞれの軸の誤差の積み重ねが、大きな誤差になる可能性があるため、作業者の練度や知識も必要になり、プログラミングの難易度も上がります。
マシニング加工のメリット・デメリット
自動工具交換装置(ATC)が付いたマシニングセンタは、フライス加工、中ぐり、穴あけ、ねじ切りなどの切削を、プログラムにより一つの機械で一連の作業を行うことで、手動の作業よりも大幅に作業効率を上げています。また段取り替えの回数も最小限になり、人的誤差や事故を防ぐことにも繋がっています。繰り返し精度も高いため大量生産にも向いており、製造業の現場に広く普及しています。
直線の3軸方向だけではなく、回転方向を加えた5軸によって刃物を動かす5軸マシニングセンタも続々と登場しており、複雑な斜面やRの加工など様々な形状の加工にも対応できます。
マシニング加工の最大のデメリットは、自動化するための複雑なプログラミングが必要になるということです。一度加工プログラムを作った後に、同じ作業を繰り返し行うのは容易ですが、最初に作業を行うときにはプログラミングに時間がかかってしまいますので、1点ずつの製作には不向きです。自動化には良い点もありますが、職人が肌感覚によって調整することが難しく、万が一問題が発生していても、そのまま気づかずに進めてしまうというケースもあります。またワイヤーやレーザーによる加工と比較して工具で物理的に金属を削るため、工具摩耗が発生して定期的なメンテナンスも必要となります。